Pressofusione
Home > Pressofusione
Come nascono i tuoi componenti in zama
Il processo produttivo di un particolare pressofuso comprende più fasi di lavorazione.
Il nostro punto di forza è il servizio “chiavi in mano”, che offre la possibilità a tutti i clienti di ottenere dei particolari in zama completamente finiti – senza ulteriori pensieri – dal momento che ci occupiamo noi di tutto.
Questo perché ogni aspetto del ciclo viene seguito internamente alla nostra azienda.
Unica esclusione le finiture galvaniche, per le quali ci rivolgiamo a partner qualificati, che lavorano, però, sempre sotto le nostre direttive.
Se ci affidi la tua produzione in serie, potrai dormire sonni tranquilli: ci occuperemo noi di tutte le incombenze produttive e ti consegneremo il tuo nuovo componente finito al 100%, proprio come lo avevi immaginato.
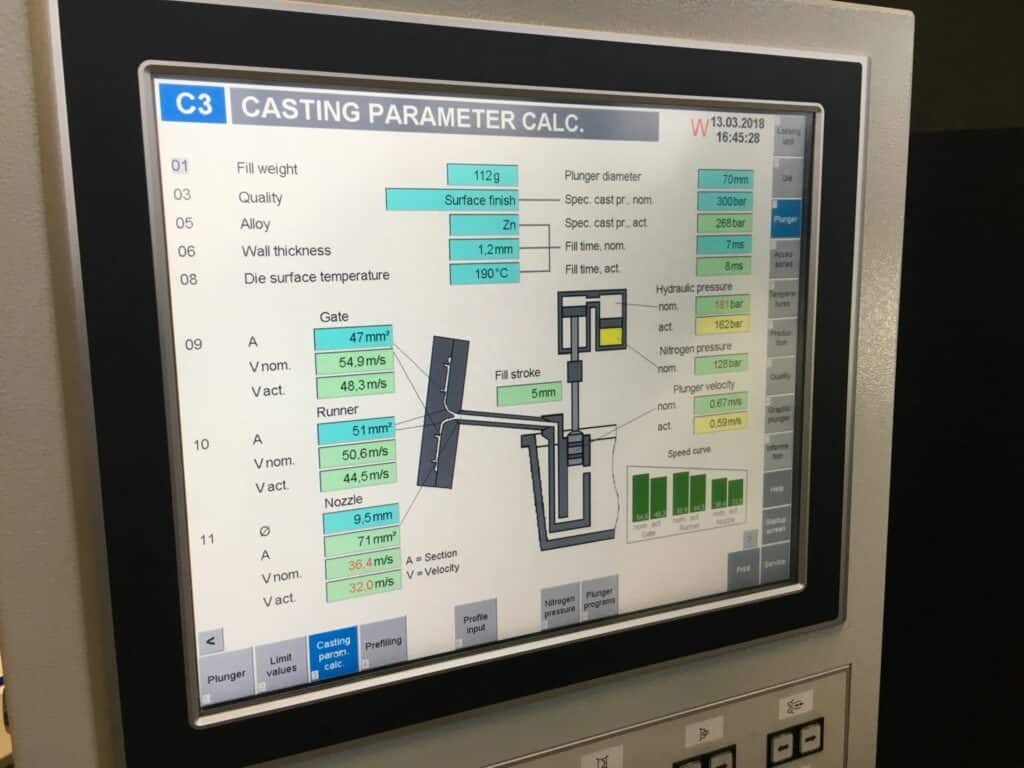
Pressofusione
Lavoriamo e stampiamo la zama mediante il procedimento di “pressofusione a camera calda”.
Siamo specialisti in questo, dal momento che ci siamo – da subito – posizionati come un punto di riferimento nella lavorazione dei componenti tecnici di precisione, realizzati con le leghe di zinco.
Infatti, la nostra azienda è nata – nel 1979 – come specialista nella pressofusione di particolari in zama dal peso di pochissimi grammi (per questo il nome originario era Micropressofusioni).
Nel tempo abbiamo poi ampliato la nostra gamma di produzione, inserendo macchine sempre più grandi.
Per questo, oggi stampiamo pezzi anche di dimensioni maggiori, dai pesi variabili tra i 0,5 grammi fino agli 800 grammi.
I particolari da noi prodotti sono impiegati in moltissimi settori, anche se – per la maggior parte – si tratta di articoli tecnici molto precisi.
In 40 anni di presenza sul mercato, abbiamo costruito ed utilizzato oltre 1800 stampi per i più svariati oggetti.
Tra i macchinari di cui disponiamo, le presse da 5 a 25 tonnellate sono state da noi sviluppate e costruite.
Questo ci ha permesso di potenziare la loro efficienza energetica e di integrare all’ interno il particolare dispositivo salvastampo, che allunga la vita dello stampo ad oltre 2.000.000 cicli e, nel tempo, va ad ammortizzare tutte le spese ad esso collegate.
L’esclusivo sistema salvastampo impedisce alla macchina di chiudere la pressa, se al suo interno è accidentalmente rimasta parte della stampata.
Questo dispositivo, abbinato all’elevata qualità costruttiva, ci permette di offrire la nostra speciale garanzia MoldCare sugli stampi da noi prodotti ed utilizzati nella fonderia, purché venga rispettato il programma di manutenzione, che va eseguito presso la nostra attrezzeria.
Quando la fase di pressofusione è completa ed i pezzi si sono raffreddati del tutto, si passa alla smaterozzatura, che può essere manuale od automatica, a seconda della grandezza e della complessità del prodotto in lavorazione.
In seguito, sui pezzi verranno eseguite le restanti operazioni, ovvero: maschiature, alesature, sabbiatura, vibrofinitura, trattamenti galvanici, ecc.
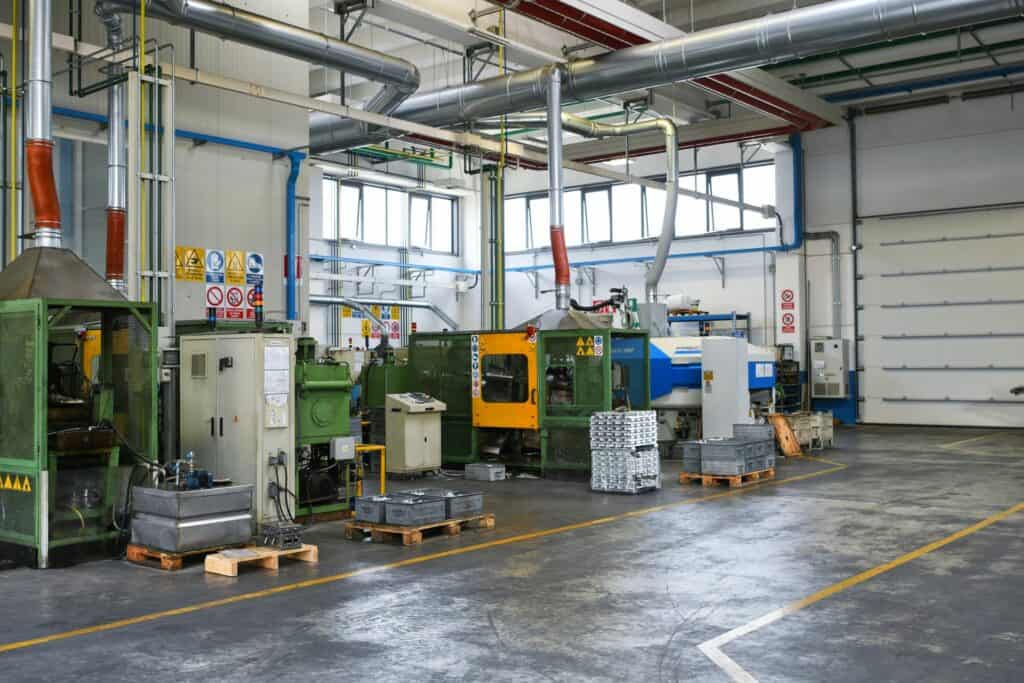
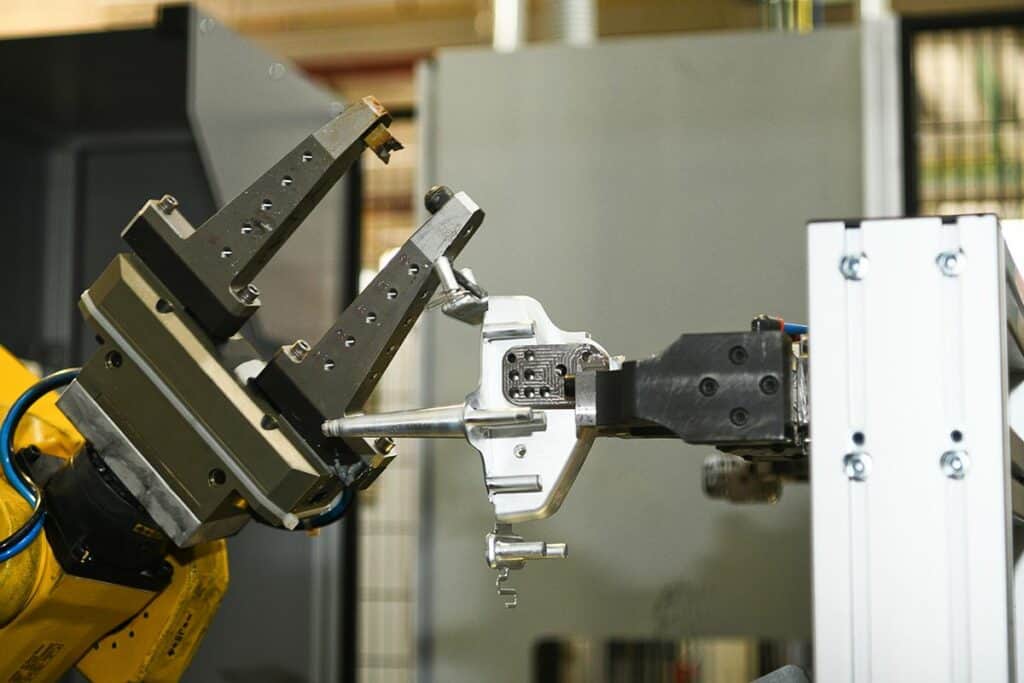
Lavorazioni di ripresa
Sempre utilizzata è la smaterozzatura: consiste nella separazione meccanica dei canali di iniezione e dei pozzetti di sfogo dal componente vero e proprio.
Nella nostra azienda questa operazione viene eseguita secondo 2 modalità principali:
- In linea: avviene subito dopo la fase di raffreddamento dello stampaggio. Può essere manuale o robotizzata, a seconda della quantità del lotto di produzione.
- In differita: attraverso dei barili rompi-colata.
A seconda delle dimensioni del componente da lavorare, si preferisce l’una o l’altra soluzione.
I pezzi in zama di piccole dimensioni si adattano bene alla smaterozzatura in differita a rotobarile, dal momento che non presentano problemi legati alla perdita di qualità, grazie alla loro massa irrisoria.
Al contrario, i componenti di medie e grandi dimensioni non sono adatti al processo di smaterozzatura a rotobarile. Se venissero sottoposti ad una violenta azione meccanica, infatti, a fine ciclo risulterebbero molto danneggiati ed inservibili. In questo caso si utilizza, allora, la smaterozzatura in linea.
Molti dei particolari che pressofondiamo vengono poi assemblati in meccanismi più complessi, tramite collegamenti filettati.
Per soddisfare le esigenze della nostra clientela e fornire i componenti finiti “chiavi in mano”, abbiamo attrezzato un intero reparto con maschiatrici automatiche e semi-automatiche.
Disponiamo di 5 filettatrici TemcoM16, molto versatili, e di 3 maschiatrici automatiche, da noi progettate e costruite per soddisfare le esigenze produttive di particolari con lotti medio-grandi.
Alcuni particolari pressofusi presentano dei fori con tolleranze molto ridotte, non ottenibili di stampaggio. In questo caso, si procede effettuando delle alesature, con un trapano a colonna.
Finiture superficiali
Per migliorare l’aspetto estetico dei particolari pressofusi in zama, andiamo ad eseguire nella nostra azienda le lavorazioni superficiali di finitura.
Queste diventano necessarie dal momento che i componenti grezzi presentano delle piccole differenze superficiali tra le varie zone del pezzo stesso, a causa dell’elevata colabilità della zama che copia fedelmente lo stampo.
Inoltre, ci permettono di uniformare il più possibile le superfici, preparando così il componente ad eventuali lavorazioni di finitura galvanica.
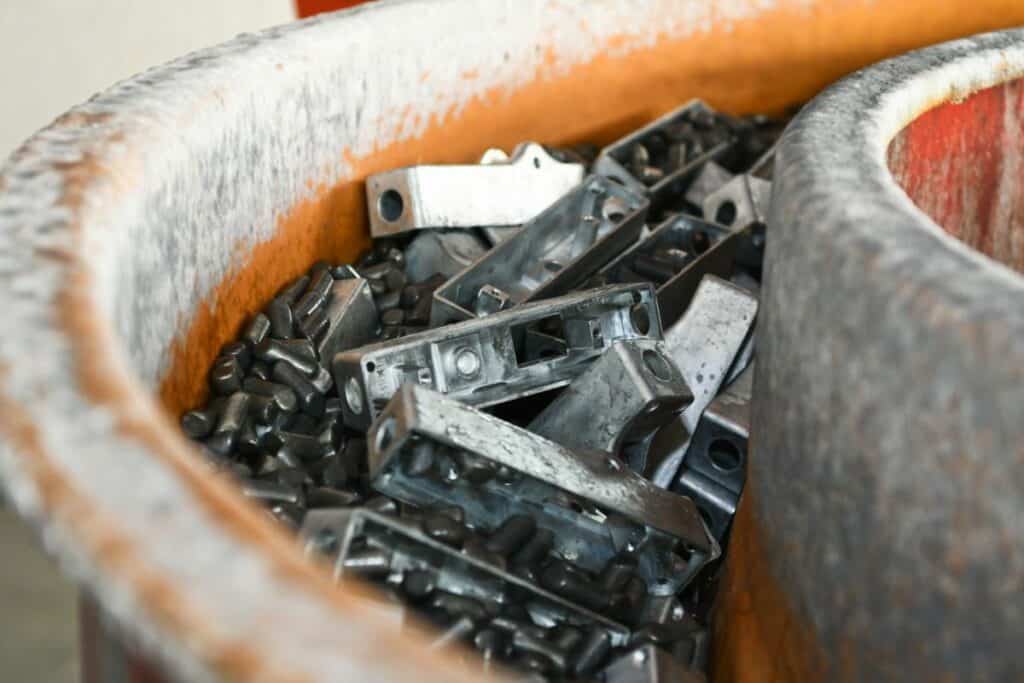
È uno dei trattamenti superficiali di maggior importanza ed è utile per eliminare anche le piccole bave – di pochi centesimi di spessore – che si possono formare durante la fase di stampaggio per pressofusione.
Granigliando i pezzi otteniamo dei particolari puliti, con superfici uniformi sia in termini di rugosità che di aspetto visivo.
Questa lavorazione aumenta anche le performance delle successive fasi di trattamento galvanico, soprattutto della zincatura.
I componenti meno delicati vengono da noi lavorati con il sistema di carico e scarico automatico, in modo da contenere al massimo i costi.
Se siamo in presenza di particolari più delicati, allora provvediamo ad un carico e scarico di tipo manuale. In questo modo, l’operatore impedirà che i pezzi si ammacchino perché eviterà l’urto, uno contro l’altro, durante questa particolare fase del ciclo.
Per maneggiare in tutta sicurezza i componenti estremamente delicati, abbiamo messo a punto un sistema di sabbiatura con effetto antiurto.
Si tratta di una particolare tecnologia che sfrutta le nostre macchine granigliatrici a rullo, offrendo risultati eccellenti a costi davvero contenuti.
Leggi qui la nostra Case History per vedere come abbiamo realizzato molti particolari sabbiati grazie a questo procedimento, riducendo così la percentuale di ammaccature fino al 95%
È il trattamento di finitura superficiale che preferiamo quando ci vengono richieste delle superfici molto lisce, che andranno poi verniciate o cromate.
È un ciclo molto più lento e costoso rispetto a quello di granigliatura, poiché è formato da più fasi: burattatura, risciacquo e asciugatura.
Per procedere con la vibro burattatura, carichiamo i pezzi all’interno della macchina e li mescoliamo a pietre abrasive, che possono avere forme differenti e vengono scelte a seconda delle caratteristiche del pezzo da lavorare.
La vibro burattatura ha quindi un ciclo che può durare anche diverse ore ma, oltre ad essere più lenta della granigliatura, ha anche un costo più elevato.
Un fattore che influisce in maniera pesante sul prezzo è la gestione della parte ambientale.
Noi abbiamo dotato la nostra azienda di un impianto di riciclo delle acque reflue, che ci permette di depurare l’acqua di modo da poterla riutilizzare anche più volte. I fanghi eliminati attraverso questo processo li smaltiamo presso aziende specializzate, il che comporta un costo elevato, ma ci garantisce il massimo rispetto dell’ambiente.
Alla fine, però, possiamo dire che – a seconda del componente da produrre – il rapporto in termini di costi vibro burattatura / granigliatura è compreso tra il 200% ed il 300%.
Per questo, noi la consigliamo soltanto nei casi in cui la burattatura si dimostri davvero indispensabile.
Trattamenti galvanici
Per proteggere la zama dai fenomeni di ossidazione – soprattutto se il componente verrà esposto ad ambienti esterni o comunque umidi – è necessario sottoporre i particolari pressofusi a dei trattamenti galvanici.
Poiché si tratta di finiture molto variegate, preferiamo rivolgerci a ditte specializzate esterne. È l’unico passaggio, dell’intero processo, che affidiamo a terzi. E, comunque, si tratta di uno step che controlliamo con estrema attenzione, affinché la lavorazione venga eseguita esattamente in linea con le nostre esigenze e, ovviamente, con quelle del cliente.
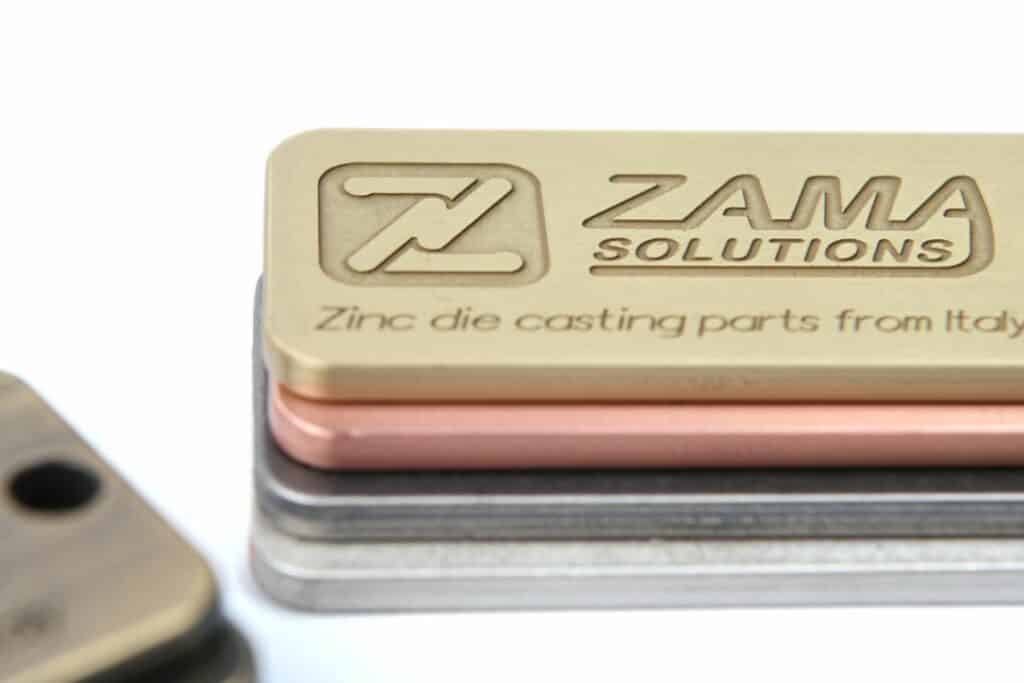
È il trattamento standard che viene eseguito sulla zama (conforme alle norme Rohs), nella variante bianca ed iridescente.
Con questo trattamento si possono ottenere protezioni in nebbia salina da 90 fino a 500 ore, a seconda dello spessore della zincatura e della presenza o meno di sigillante.
La zincatura trivalente può essere eseguita a rotobarile, e questa rappresenta la soluzione più economica tra i trattamenti galvanici.
Di solito è adatta a particolari di piccole e medie dimensioni.
Per i componenti più delicati, consigliamo invece la zincatura eseguita staticamente a telaio.
Si tratta di un processo più costoso, ma garantisce un risultato di qualità nettamente superiore rispetto al trattamento a rotobarile.
Ad ogni modo, la funzione della zincatura è soprattutto antiossidante e non estetica. Per questo, tra i vari pezzi, non si cerca l’uniformità di colorazione.
Anche altri trattamenti sono possibili su richiesta, ma la nichelatura e la cromatura sono i più diffusi.
Entrambe le finiture hanno funzione protettiva e offrono al contempo maggiori uniformità estetiche.
Anche qui, i particolari si possono lavorare a telaio o rotobarile, a seconda della loro grandezza e delicatezza.
I trattamenti di nichelatura e cromatura sono più costosi rispetto alla zincatura, dal momento che il ciclo di lavorazione diventa più complesso ed anche i materiali utilizzati hanno un prezzo di partenza alto.
Ad ogni modo, se non ci sono particolari esigenze estetiche, noi consigliamo di orientarsi sempre verso la zincatura. Non solo perché è più economica, ma anche perché la zincatura ha meno restrizioni dal punto di vista ambientale.
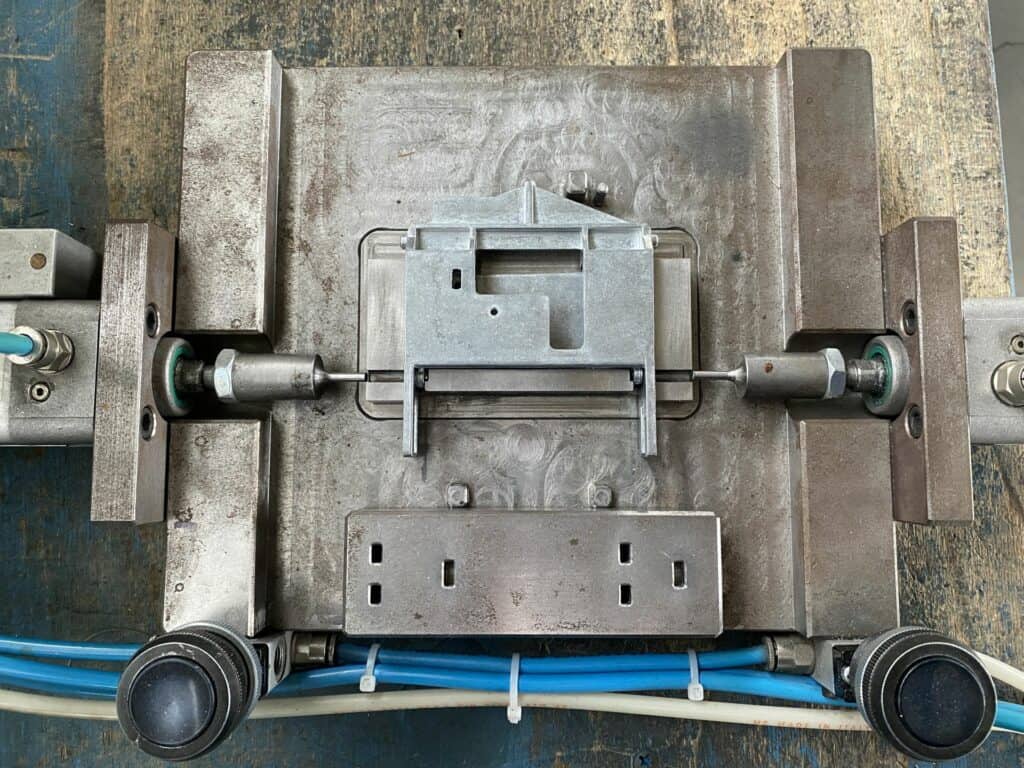
Assemblaggi
Per soddisfare al meglio tutte le esigenze della nostra clientela, effettuiamo anche piccole lavorazioni di assemblaggio sui nostri particolari pressofusi.
Anche se il core business di Zama Solutions è la vera e propria pressofusione, siamo in grado di offrire un servizio completo “chiavi in mano” ai nostri clienti, fornendo loro particolari già pre-assemblati, se richiesto.
Dal momento che si tratta di lavorazioni molto delicate, nel nostro ufficio tecnico studiamo sia le procedure che le attrezzature necessarie per ottenere il risultato voluto.
Regolarmente, eseguiamo anche premontaggi di viti o grani, piantaggi di cuscinetti o spine, ecc.
Magazzino e logistica
Al termine del processo produttivo, i pressofusi giungono nel nostro reparto magazzino.
Qui li prepariamo per le spedizioni o li sistemiamo in fase di stoccaggio, nel caso in cui si tratti di materiale di scorta.
A seconda del tipo di componente, i pressofusi vengono imballati in svariate tipologie di contenitori.
La minuteria viene generalmente confezionata all’interno di cassoni metallici, nel caso di grandi lotti, oppure in scatole di cartone a perdere, nel caso di piccoli lotti.
Se richiesto dal cliente, possiamo offrire anche un servizio di personalizzazione degli imballaggi, con grafica e loghi forniti dallo stesso committente.
In questo modo, il cliente non dovrà preoccuparsi di nulla, tanto meno di fare delle lavorazioni aggiuntive su prodotti già finiti.
Nel caso in cui i nostri componenti siano particolarmente delicati – soprattutto se hanno subito o subiranno dei trattamenti estetici – sovente predisponiamo dei termoformati o altri tipi di imballaggio dedicati, in modo da proteggere i pezzi ed evitare degli urti accidentali tra di loro, sia durante la movimentazione, sia durante il trasporto.
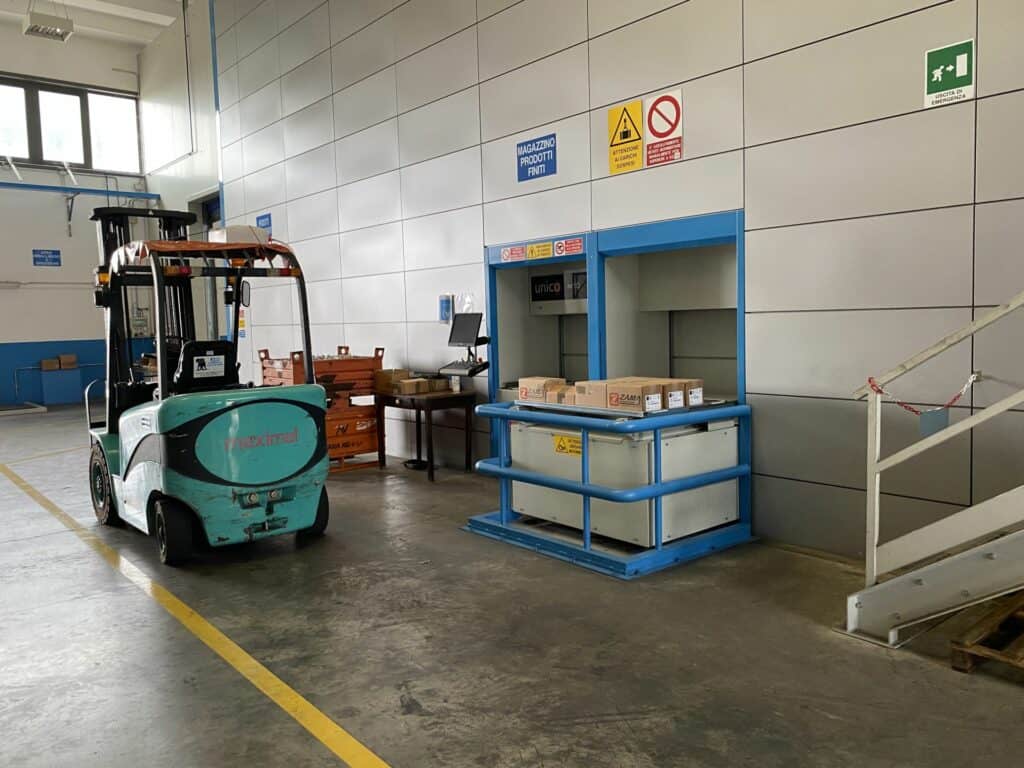
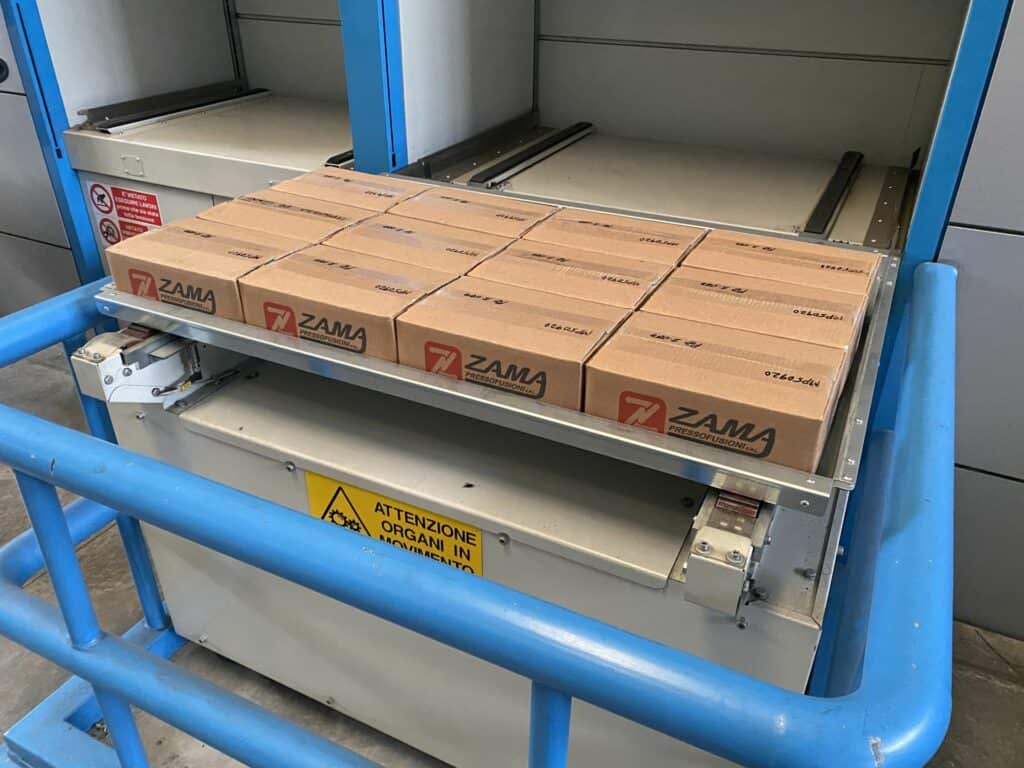
Forniamo anche un servizio extra di gestione delle scorte concordate, facendole ruotare a seconda delle esigenze. Questo è un grande vantaggio per i nostri clienti, perché va ad accorciare in modo notevole le tempistiche di consegna.
Anche per questo, abbiamo di recente installato un magazzino verticale di generose dimensioni.
Al suo interno i contenitori vengono caricati in appositi cassetti, riposti poi automaticamente in ripiani all’interno della struttura.
Questo impianto è collegato in rete con il nostro software gestionale. Ogni movimento di deposito e prelievo viene quindi registrato, in modo da tracciare ed aggiornare in continuazione il nostro inventario.
Abbiamo anche implementato delle personalizzazioni che ci permettono di gestire con maggior efficacia la rintracciabilità dei lotti.
Per questo, ogni singolo contenitore o scatola che esce dal magazzino dispone di un codice univoco registrato a sistema. È come una sorta di “carta d’identità” del prodotto, grazie alla quale si può risalire a tutta una serie di informazioni, come ad esempio quelle relative ai controlli di qualità di quella commessa specifica.
Le spedizioni sono quotidiane e, per effettuarle, ci serviamo di mezzi propri o di trasportatori convenzionati.
Noi di Zama Solutions siamo trai pochi fornitori di componenti in zama che, ascoltando una tua semplice idea, riusciamo a trasformarla in un articolo finito e lo depositiamo direttamente tra le tue mani!
Ogni tuo progetto, grazie al nostro aiuto, prende subito forma e diventa una produzione in serie completa, ottimizzata e performante.
Se non desideri altro che affidare il lavoro della tua azienda a professionisti esperti e qualificati, contattaci adesso!
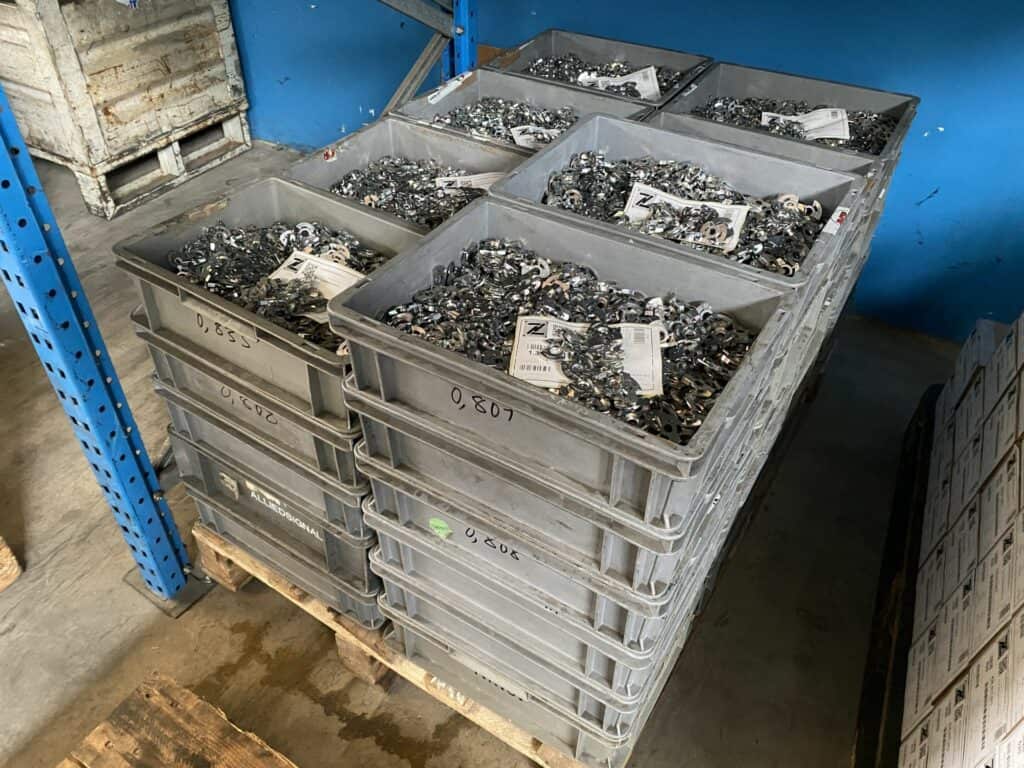
Hai un nuovo progetto? Parliamo assieme! Fissa adesso una video call con il nostro staff