Stampi
Home > Stampi
In Zama Solutions da oltre 40 anni costruiamo stampi solo per la zama e ci dedichiamo alla lavorazione esclusiva delle leghe di zinco.
Il nostro punto forte è quindi la grande esperienza nel settore, unita ad una forte specializzazione nel mondo della zama.
Nello specifico, siamo esperti di componenti tecnici dall’ elevata complessità e con tolleranze molto strette.
Gli stampi che produciamo sono quindi molto accurati e di estrema precisione, perché ogni singolo elemento è da noi studiato e realizzato con un’attenzione costante alle fasi successive dell’intero processo produttivo.
Dopo aver progettato uno stampo si passa alla sua fabbricazione.
Gli stadi necessari per arrivare al risultato finale sono numerosi, anche per questo ci avvaliamo di più figure tecniche esperte di queste fasi, per monitorare ed ottimizzare ogni singolo passaggio.
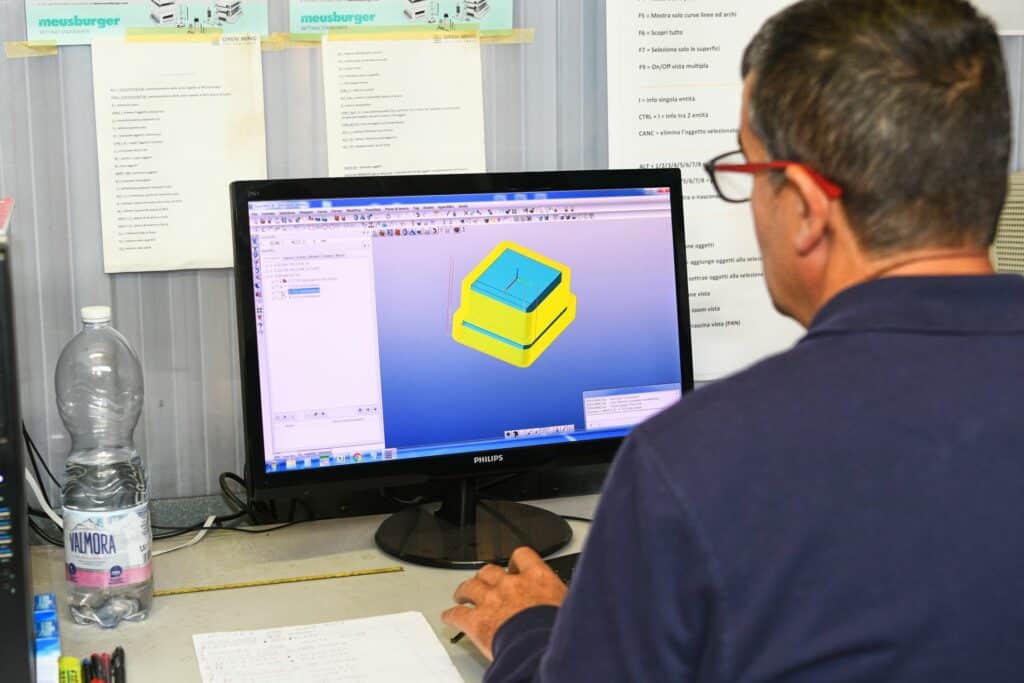
Percorsi utensili matrici e portastampi
La prima fase successiva alla progettazione prevede il calcolo dei percorsi utensili di fresatura.
Il percorso utensile è il programma che la macchina a controllo numerico deve compiere per creare il pezzo.
In questa fase ci avvaliamo di Hypermill di Open Mind, un potente software che ci permette di sfruttare al massimo le potenzialità dei centri di lavoro, fino ai 5 assi.
Questo software è così avanzato da venir utilizzato a vari livelli della Formula 1, in ben 9 scuderie su 10.
Per il calcolo del percorso utensile utilizziamo, invece, appositi database, che ci forniscono le soluzioni migliori a seconda del componente: dalle procedure da adottare agli utensili più indicati.
A questo punto, eseguiamo il vero e proprio calcolo del percorso utensile ed esaminiamo a video il risultato, per fare le dovute ottimizzazioni.
Facciamo, inoltre, una simulazione virtuale della lavorazione, per verificare ancora una volta la correttezza di quanto calcolato.
Infine, post-processiamo il percorso utensile, ovvero facciamo in modo che il software CAM traduca il percorso in un linguaggio comprensibile alla macchina sulla quale eseguiremo il programma. Questo verrà poi trasferito direttamente in macchina tramite la rete ethernet aziendale.
Fresatura CNC delle matrici
Dopo aver preparato il percorso utensile, lo andiamo ad eseguire sui centri di lavoro.
In Zama Solutions disponiamo di 5 centri di fresatura CNC: 4 ad alta velocità, di cui 2 a 5 assi.
Queste macchine ci permettono di produrre buona parte dei componenti necessari per costruire lo stampo.
Di solito, per avviare la fresatura, si inizia con il piazzamento e l’allineamento del pezzo da lavorare.
Si prosegue, poi, con il caricamento e la misurazione di tutti gli utensili che verranno utilizzati.
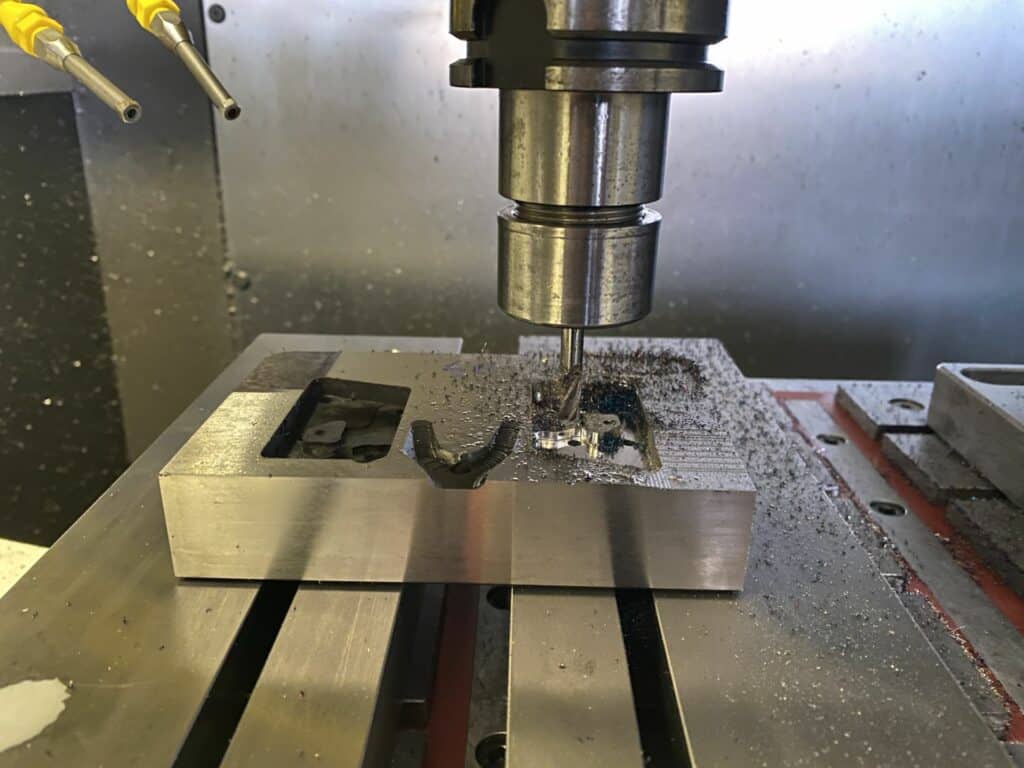
Quindi, si parte con la lavorazione vera e propria, adoperando il programma che abbiamo precedentemente calcolato con l’apposito software e trasmesso in macchina.
Se bisogna eseguire delle forature o spianature, queste vanno realizzate a bordo macchina, appena prima del lancio della lavorazione stessa.
Terminata l’esecuzione, misuriamo il pezzo direttamente sulla macchina. In questo modo possiamo essere sicuri della bontà della lavorazione prima di rimuovere il prodotto.
Inoltre, quando facciamo delle copiature per degli accoppiamenti di 2 tasselli, verifichiamo direttamente in macchina l’accoppiamento degli stessi, in modo da essere certi che lo stampo non generi bave durante la fase di pressofusione.
Questo è importante, perché la zama è un materiale molto fluido, e tende a fare bava già con giochi sullo stampo di 0,02 mm.
È proprio prestando attenzione ad ogni minimo dettaglio, che in Zama Solutions ci assicuriamo di ottenere uno stampo dalle elevate prestazioni e con un’ottima precisione produttiva.
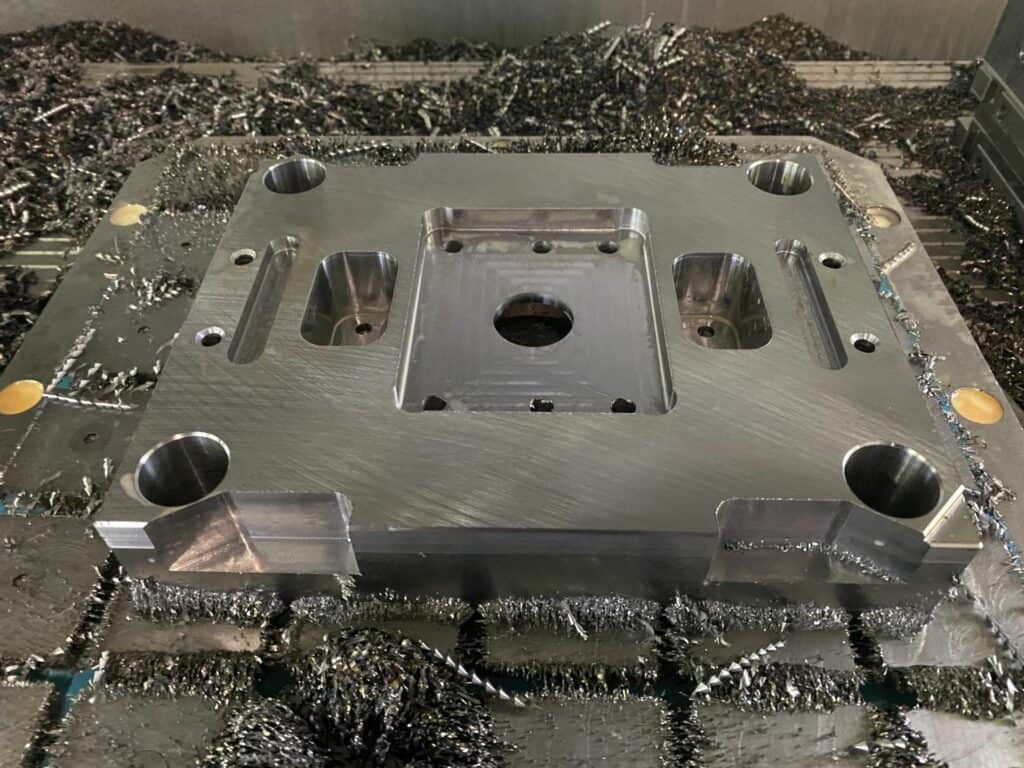
Fresatura dei portastampi
La costruzione del portastampo è una fase molto delicata perché è fondamentale per il corretto funzionamento dello stampo e per la precisione ottenibile sul prodotto finale.
Ad ogni modo, è composto da singole parti piuttosto semplici da realizzare.
Partiamo da basi “normalizzate”, ovvero semilavorate, che sono versatili e precise, e risultano reperibili in commercio in forme, dimensioni e materiali diversi.
Su queste, per prima cosa eseguiamo le forature, che servono per alloggiare le viti di fissaggio dei tasselli figura.
Terminati i fori, si sgrossano le sedi per i tasselli ed i piani di scorrimento di eventuali cassetti.
Di seguito si eseguono i processi di finitura, che vengono eseguiti su un’ altra macchina estremamente precisa, perché poi il risultato di questi passaggi determinerà l’accuratezza dello stampo e di conseguenza del componente finale.
Si tratta di un passaggio davvero importante, perché se non eseguito correttamente rischiamo di ritrovarci degli sfalsamenti sulle chiusure stampo, sgradevoli a livello estetico ma soprattutto non accettabili dal punto di vista funzionale e dimensionale.
Dopo che abbiamo preparato le sedi dei tasselli, eseguiamo i circuiti di raffreddamento ed i fori di alloggiamento delle colonne inclinate di eventuali movimenti a cassetto.
Infine, dopo un’accurata analisi e misurazione delle lavorazioni fatte, si procede alla rifinitura manuale delle piastre, rendendole disponibili per l’assemblaggio finale.
Trattamenti termici
- Abbatte i tempi di lavorazione;
- Annulla le spese di trasporto;
- Elimina il rischio di smarrire per strada dei semi lavorati e dover rifare tutto il lavoro da capo.
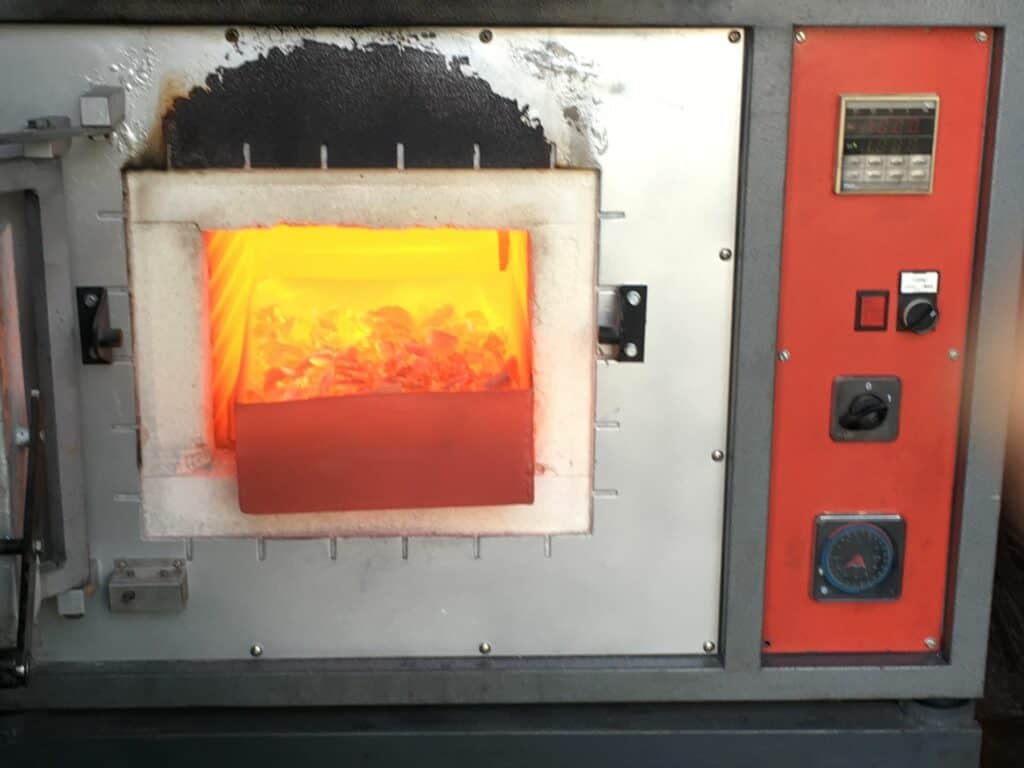
Rettifica
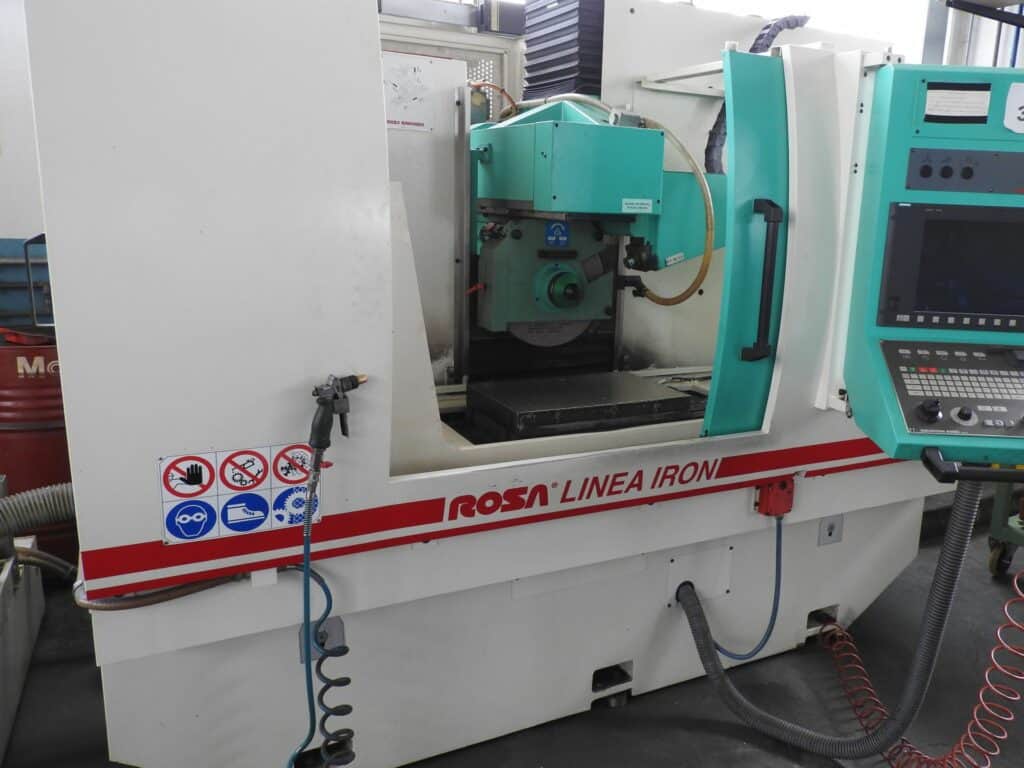
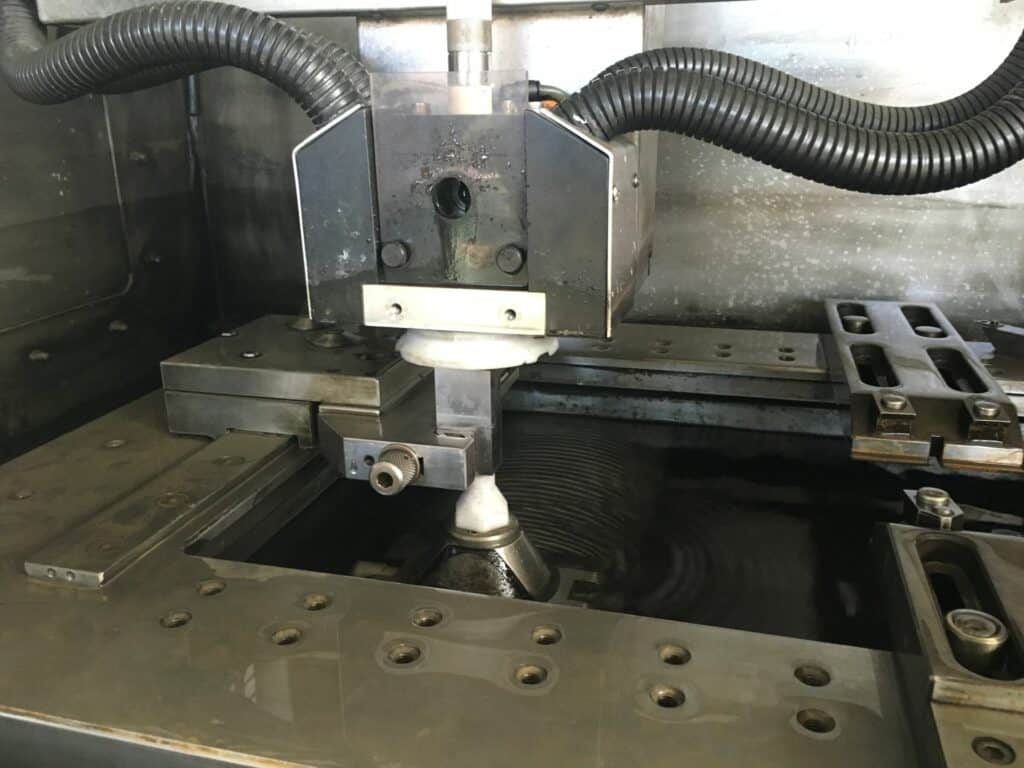
Elettroerosione a filo
Elettrodi
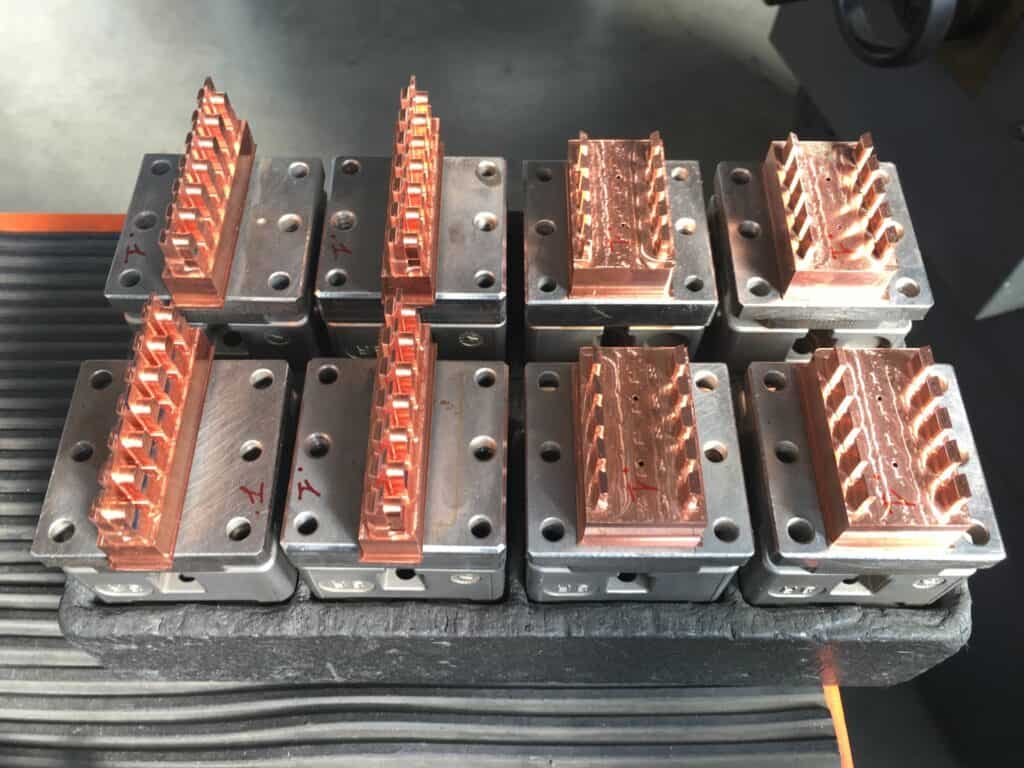
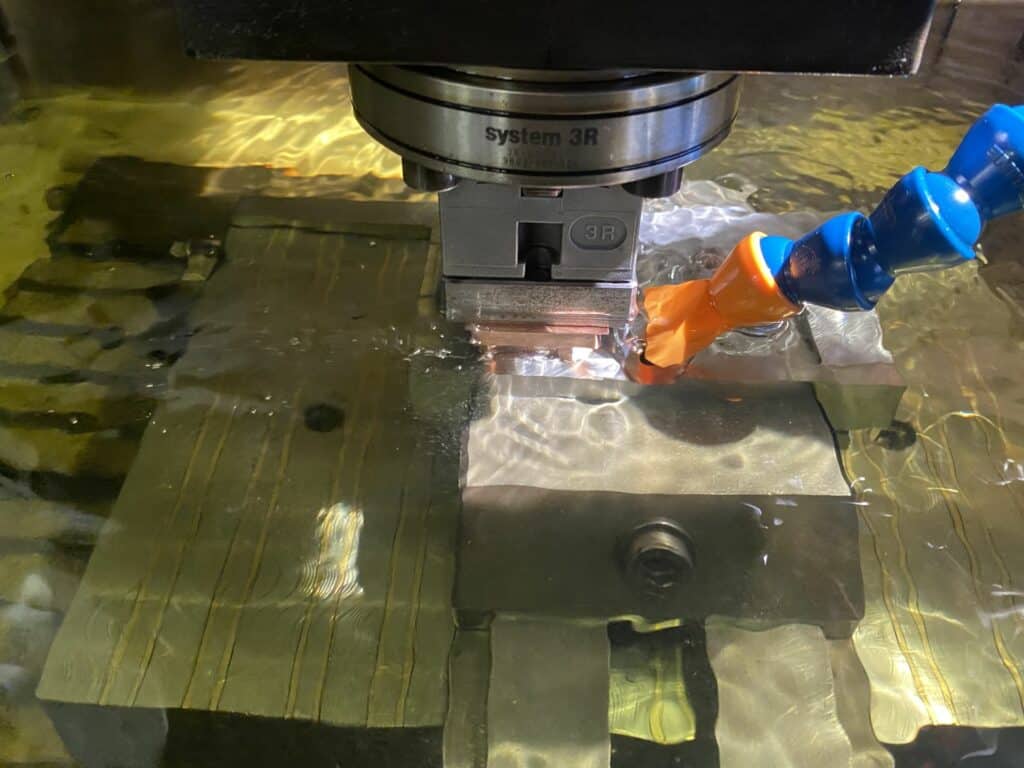
Incisione delle figure
Questa lavorazione si serve della tecnologia detta “elettroerosione a tuffo”.
Si tratta di una macchina che scava l’acciaio mediante scariche elettriche controllate, che passano dall’elettrodo al pezzo, secondo un preciso programma prestabilito.
Alla fine, si ottiene un’incisione al negativo perfettamente fedele all’elettrodo utilizzato.
Ovviamente, la qualità dell’incisione dipende dalla qualità di realizzazione dell’elettrodo.
Per questo, prima di procedere, noi li rifiniamo tutti con attenzione, eliminando le sbavature e lucidandoli alla perfezione.
Una volta pronti, li carichiamo nella macchina e li allineiamo, facendo poi lo stesso con il pezzo da produrre.
Si lancia così il programma e si lascia lavorare la macchina in modalità non presidiata.
Terminato il processo, si utilizzano appositi strumenti di misura in dotazione alla macchina, per fare i rilievi del caso e validare la lavorazione.
Si provvede a rimuovere il pezzo dalla macchina e lo si avvia alle successive fasi di aggiustaggio ed assemblaggio.
Aggiustaggio e assemblaggio
Una volta che i componenti dello stampo sono pronti, vengono assemblati tra di loro.
Per prima cosa bisogna fare alcune verifiche:
- Si provano le chiusure.
- Si ritoccano i componenti, se necessario.
- Si controlla la lucidità delle figure, per evitare la formazione di piccoli sottoquadri, responsabili di deformazioni e rigature sui pezzi stampati.
Appena è tutto pronto, si assembla lo stampo.
E a quel punto lo si può consegnare alla fonderia per la prima prova stampo.
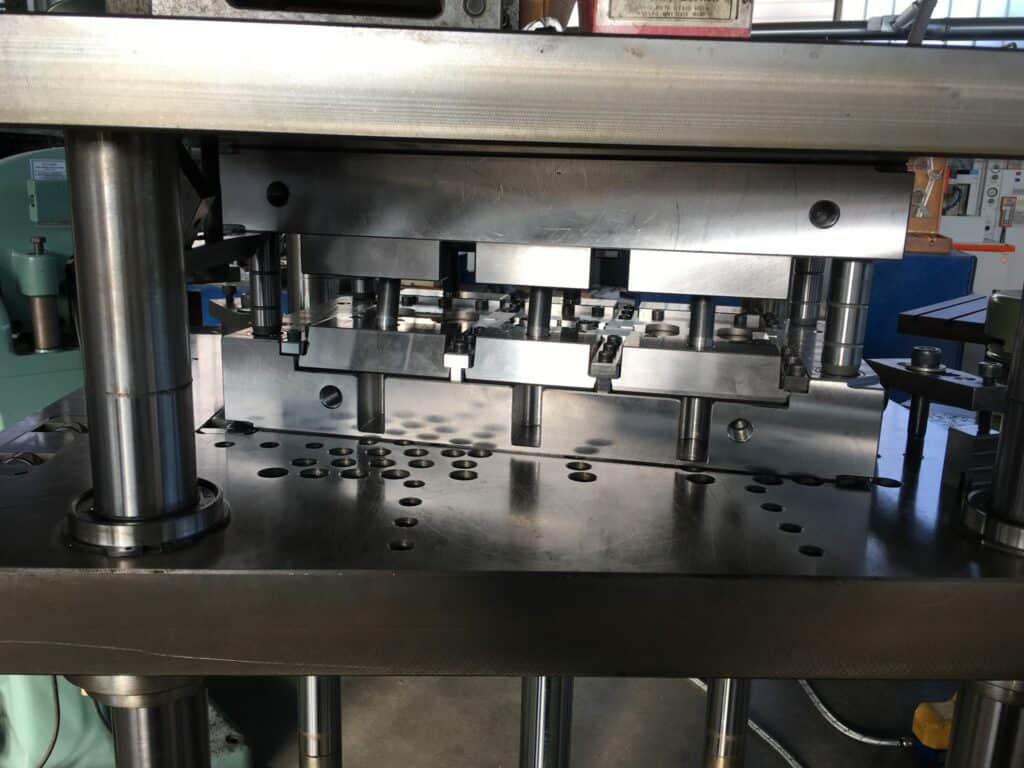
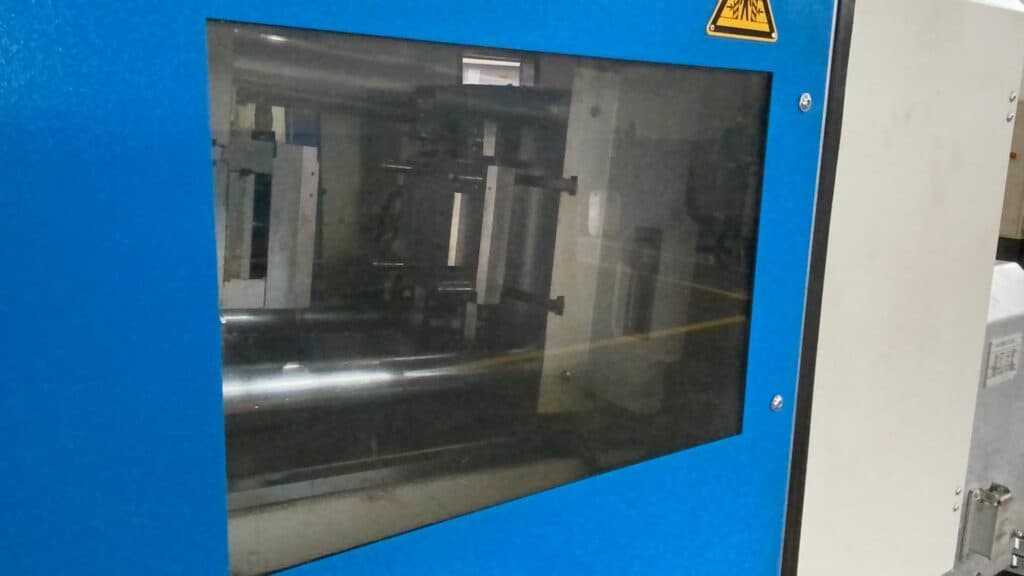
La prova stampo
Quando finalmente lo stampo è pronto, arriva il momento tanto atteso: il montaggio in macchina per la prima volta.
Inizia così la “prova stampo” che può essere relativamente semplice nel caso di uno stampo standard, o piuttosto complessa in altre situazioni.
Dopo un piccolo rodaggio per assestare i componenti, si dà il via alla vera e propria prova.
La prova stampo consiste nel produrre circa 50 stampate, che possono anche aumentare di numero a seconda degli accordi presi con il cliente.
Terminata la prova, si procede con la stesura di un Report, nel quale si riportano le eventuali problematiche riscontrate, in modo da facilitare la successiva messa a punto in attrezzeria.
Il collaudo dei campioni
L’ultima parte del processo di costruzione di uno stampo prevede il collaudo dei campioni: serve a validare il lavoro fatto e predisporre eventuali messe a punto.
Per eseguirlo correttamente bisogna produrre una versione pallinata del disegno quotato del componente, dopo di che si passa alla misurazione dei pezzi.
Durante questa operazione, generiamo sempre un Report da consegnare al cliente.
Terminati i rilievi, si procede con la preparazione del campione e l’imballaggio.
Di solito i campioni vengono consegnati grezzi, poiché eseguiamo giusto le lavorazioni di ripresa concordate, per accelerare i tempi di consegna dei primi esemplari.
Può capitare che dopo aver esaminato i campioni, sia necessario procedere con eventuali aggiustamenti, come le messe a punto richieste, portare in tolleranza le quote, o risolvere altri piccoli problemi rilevati durante la nostra prova.
Appena sistemato il tutto, se richiesta dal committente, si può eseguire un’ulteriore prova stampo ed un altro rilievo.
Appena il cliente ci darà la sua approvazione – una volta ricevuti i campioni – partiamo con la produzione in serie.
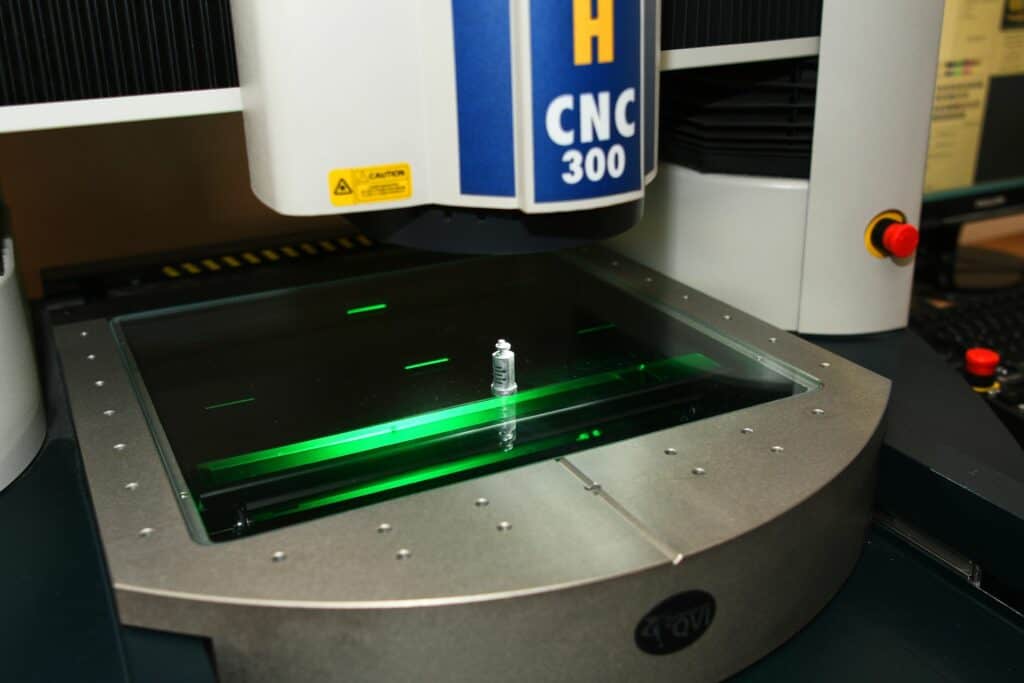
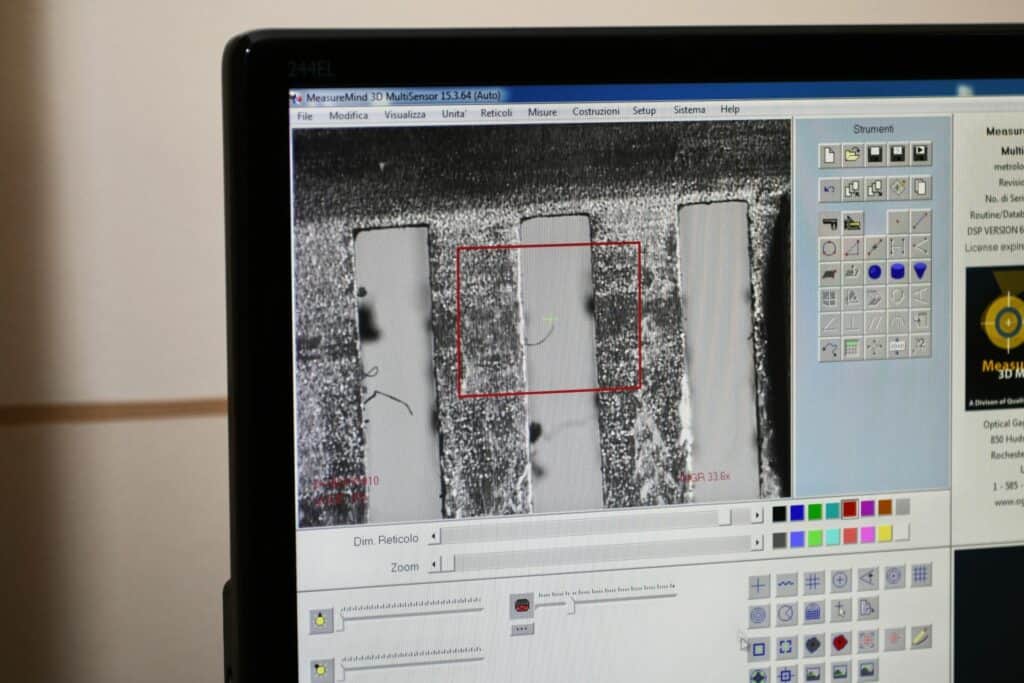
A questo punto, se abbiamo gestito il processo in modo corretto, i campioni risulteranno impeccabili. In caso contrario, si dovrà andare ad indagare a ritroso la causa di un errato risultato.
Noi, in realtà, non ci preoccupiamo più della prova stampo, perché – salvo casi davvero rarissimi – ci convalida nella maggior parte dei casi la qualità dei nostri componenti. È in pratica una conferma dell’aver svolto in modo corretto e preciso il nostro lavoro.
La serenità di superare tutte le prove stampo ed il collaudo dei campioni l’abbiamo ottenuta dopo anni di studi e prove sul campo, realizzando il nostro sistema unico ZINCode: il primo metodo di analisi, da noi stessi messo a punto, che permette di risolvere fin da subito – ovvero a partire già dal progetto su carta – oltre al 97% delle problematiche di processo produttivo.
Comprese quelle legate alla produzione dello stampo.
Infatti, i nostri dati degli ultimi 4 anni hanno riportato che:
- Il numero massimo di quote da sistemare dopo la prima prova stampo si è ridotto (è sempre inferiore alle 5).
- Non vengono eseguite più di 2 prove stampo per avere un pezzo conforme.
- La percentuale media dei lotti conformi sul totale di quelli prodotti negli ultimi 4 anni ha superato il 99,3 % (dato documentato dal sistema ISO 9001).
Questo si traduce per i nostri clienti, in un risparmio di tempo, soldi e maggior fiducia nei nostri confronti.
E quindi, chi lavora con noi sa che mettiamo a disposizione non solo la nostra competenza tecnica ed esperienza, ma un vero e proprio metodo scientifico di analisi strumentale utile ad ottimizzare il processo.
Di conseguenza, anche gli stampi risultano più performanti e più longevi nel tempo.
Hai un nuovo progetto? Parliamo assieme! Fissa adesso una video call con il nostro staff