Se ti stai chiedendo come riconoscere la zama, dove si trova e quando è più conveniente utilizzarla, ti sarà tutto più chiaro una volta comprese a fondo le sue caratteristiche chimico-fisiche e anche quelle meccaniche.
Viene infatti utilizzata in tutte quelle situazioni in cui sono richieste le sue proprietà come: durezza, resistenza, peso specifico, limitata corrosione ne tempo, facilità di lavorazione, ecc.
Essendo una lega chimica, le sue proprietà sono influenzate sicuramente dallo zinco, responsabile delle caratteristiche principali, poiché determina soprattutto la densità della zama ma anche il peso specifico della zama, e molto altro.
Trattandosi di una lega di zinco e non del materiale puro, ci sono però anche altri componenti che partecipano alla formulazione e ne influenzano le proprietà.
Se il peso specifico dello zinco è più o meno sempre mantenuto, i metalli che vengono aggiunti possono andare ad influenzarne la resistenza, la durezza, ecc.
In effetti, quando si parla di zama, sarebbe più corretto classificarla come una “famiglia di leghe”, dal momento che esistono più tipologie.
Gli appartenenti a questa famiglia si differenziano tra loro per le concentrazioni percentuali di ciascun elemento legato allo zinco. Si può avere infatti, una lega di rame e zinco, una lega di zinco e alluminio, ecc.
Abbiamo così le leghe stampabili a camera calda la Zama 2 (ZP2), la Zama 3 (ZP3), la Zama 5 (ZP5) e la Zama 8 (ZP8).
Esistono poi anche la Zama 12 (con il 12% di alluminio) e la Zama 27 (con il 27% di alluminio). Queste due leghe sono stampabili solo a camera fredda, perché le alte percentuali di alluminio in esse contenute innalzano la temperatura di fusione a tal punto da non rendere possibile il processo a camera calda.
Il punto di fusione dell’alluminio è infatti molto più alto rispetto a quello dello zinco o del punto di fusione del rame, ecc. Quindi leghe con alte concentrazioni di questo metallo andranno lavorate con un processo diverso.
Quando scegliere una lega di zama piuttosto che l’altra?
Dipende tutto dalle esigenze di progettazione e dal risultato finale che si vuole ottenere.
- La ZP3 e la ZP5 sono quelle più utilizzate. Entrambe hanno un’elevata stabilità dimensionale, ma la ZP3 ha una miglior resistenza alla corrosione, mentre la ZP5 è da preferire se si vuole ottenere una resistenza all’impatto davvero alta.
- La ZP2 è quella con caratteristiche meccaniche migliori, ma tende ad invecchiare più facilmente delle altre.
- La ZP8, invece, offre una resistenza e una durezza del componente davvero elevate, ma di fatto non ha molto mercato a causa del costo elevato richiesto, per il materiale stesso e per la sua lavorazione.
Lavorare con una lega – anziché un metallo puro – offre diversi vantaggi.
Il sistema zinco-alluminio, al quale vengono poi abbinate piccole percentuali di altri elementi, permette di esaltare una caratteristica piuttosto che l’altra, a seconda delle esigenze.
Facciamo un esempio: se aggiungiamo allo zinco l’alluminio – fino al 4,5%, altrimenti otteniamo l’effetto contrario – possiamo abbassare il punto di fusione.
Cosa vuol dire questo?
Che utilizzando la zama – anziché lo zinco puro – puoi risparmiare. Questo perché la quantità di calore richiesta per rendere la zama liquida, e quindi lavorabile, risulta inferiore a quella necessaria per fondere il metallo puro.
E il tutto si traduce in un bel vantaggio economico.
Oppure, sempre aggiungendo l’alluminio – e ancora meglio se ci abbini una piccola percentuale di rame – potresti aumentare la resistenza e la durezza dei tuoi componenti qualora il progetto lo richiedesse.
E così via.
Grazie alla conoscenza di come influisce ciascun elemento chimico su ognuna delle caratteristiche della lega, possiamo scegliere le percentuali più adatte per ottimizzare la lavorazione di un prodotto e modellare le sue qualità secondo le nostre esigenze.
Riassumo in uno schema le composizioni principali delle leghe di zinco:
ZP3 (ZnAl4) | ZP5 (ZnAlCu3) | ZP2 (ZnAl4Cu3) | ZP8 (ZnAl4Cu1) | |
Alluminio % | 3.7 – 4.3 | 3.7 – 4.3 | 3.7 – 4.3 | 8.0 – 8.8 |
Rame % | 0.1 | 0.7 – 1.2 | 2.7 – 3.3 | 0.8 – 1.3 |
Magnesio % | 0.025 – 0.05 | 0.025 – 0.05 | 0.025 – 0.05 | 0.015 – 0.03 |
Zinco% | resto | resto | resto | resto |
Per comprendere meglio questo schema e capire nel dettaglio come ogni singola aggiunta possa modificare le caratteristiche della lega, bisogna studiare l’influenza determinata dai fattori chimici presenti.
Ti vorrei ricordare che quanto riportato nel mio blog fa sempre riferimento alla normativa attualmente in vigore. In particolare per questo argomento vorrei citare come fonte le Norme UNI EN 1774.
Vuoi conoscere tutte le caratteristiche della zama e scoprire i singoli vantaggi che può offrire ai tuoi componenti? Scarica ora la mia guida GRATUITA “Leghe di zinco”
Ogni elemento della zama può fare la differenza per i tuoi componenti.
Vediamo ora un semplice schema in cui sono riportati i pro e contro dell’aggiunta di ogni singolo componente.
Per prima cosa analizziamo gli effetti dell’alluminio:
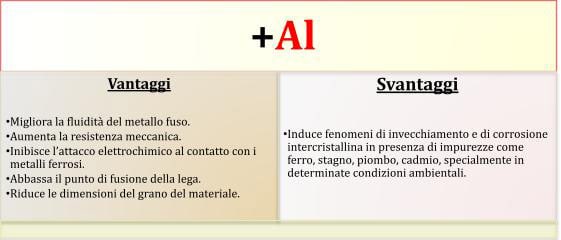
La bassa temperatura di fusione, l’elevata colabilità e l’alta stabilità dimensionale rendono la zama adatta alla realizzazione di componenti anche molto complessi.
L’alluminio, assieme allo zinco, è un elemento sempre presente nella composizione della zama.
Da qui emerge il suo ruolo primario all’interno delle leghe.
L’aggiunta dell’alluminio, infatti, offre due vantaggi fondamentali:
- Permette di risparmiare sulla quantità di calore necessario a fondere il materiale per lavorarlo.
- Aumenta la fluidità della materia prima e per questo rende la fase di stampaggio più semplice e precisa.
Passiamo ora al Rame:
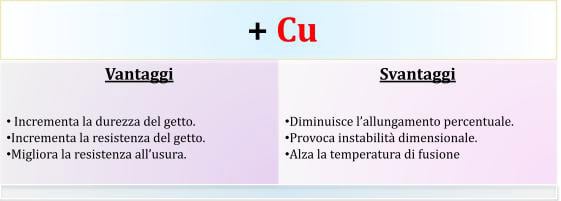
Anche il rame aumenta notevolmente la durezza e la resistenza del componente, ma in questo caso ne riduce la stabilità e la durata nel tempo.
E infine il magnesio:
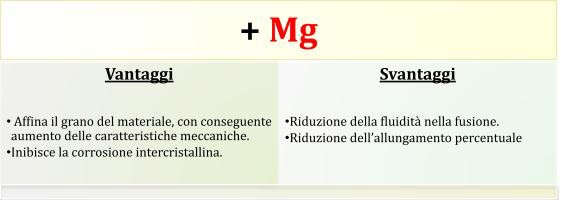
Attenzione alle impurezze della zama.
Ci sono poi altri elementi che possono essere presenti in piccolissime percentuali e vengono considerati come estranei, perché non graditi.
Si tratta delle così dette “impurezze”, ovvero elementi le cui proprietà all’interno della lega non vengono apprezzate ai fini produttivi.
Se non è possibile eliminarli del tutto, si cerca di mantenerli in concentrazioni davvero minime.
Vediamo allora quali sono i principali elementi che vengono considerati impurezze nel caso della zama:
- Ferro
È ammessa una concentrazione massima dello 0,05%.
Aumenta la fragilità della lega, a causa della formazione di scorie che si possono inglobare nel getto. Se presente in alte quantità, forma degli intermetallici con l’alluminio. - Piombo
È ammessa una concentrazione massima dello 0,005%.
Esso induce la lega all’invecchiamento precoce, provoca cricche e distorsioni nel getto, oltre che corrosione intercristallina. - Cadmio
È ammessa una concentrazione massima dello 0,005%.
È responsabile di una diminuzione delle proprietà meccaniche e induce la corrosione intercristallina. - Stagno
È ammessa una concentrazione dello 0,002%.
È il responsabile della creazione di intermetallico con l’alluminio. Peggiora, inoltre, la lavorabilità all’utensile.
Come puoi ben immaginare, per essere sicuri di avere un basso il livello di impurezze è fondamentale rivolgersi ad un fornitore di materia prima affidabile e certificato.
Io stesso mi accerto personalmente del costante controllo eseguito nei laboratori dei miei fornitori su ciascun lotto di materie prime, nel rispetto delle restrittive normative italiane e come garanzia di alta qualità della zama con la quale sono solito lavorare.